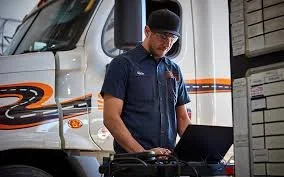
thought leadership: logistics industry
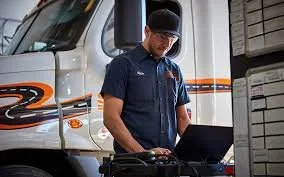
Addressing the Critical Diesel Technician Shortage
Decisiv SRM Offers a Proven Strategy to Win the Talent Wars
By Dick Hyatt, CEO & President, Decisiv, Inc.
It’s no secret that the diesel technician field has suffered from a widespread, chronic shortage of technicians -- a shortage that’s hurt both dealers and customers in terms of asset downtime and lost revenue.
The good news is, some major players have seen the light, and are stepping up to feed the growing technician pipeline. Many OEMs have established partnerships with diesel technology programs to fund scholarships and provide on-the-job training opportunities. One such program involves Daimler Trucks North America teaming up with Universal Technical Institute in Arizona on the 12-week-long DTNA Finish First elective that provide hands-on training for technicians. And Volvo Trucks and Mack Trucks are working with Western Technical college in El Paso, Texas, offering advanced diesel technician training programs. In fact, Decisiv is advising the Western Tech-Volvo-Mack partnership, working to include an ASIST module in the curriculum.
What does that mean for the industry? Like it or not, it means there’s no going back to the way the diesel maintenance and repair business used to be. Streamlined, modern shops are in the process of replacing traditional paper-dependent shops. And the incoming waves of new techs will have been trained in paperless work environments. They’ll feel as comfortable with laptops and tablets as they are with wrenches and the smell of motor oil.
By now, you might be thinking, Decisiv is a tech company. Of course, a tech company wants my operation to go high-tech.
My response to that is, Yes – Decisiv wants to help your operation have a smooth, manageable transition to the inevitable change that’s coming.
Here’s why:
The resistance to going to paperless is real. (Very real.) And it’s rooted in the perception that making the change will be too difficult. That it will feel too foreign, and take too long for all the players to get comfortable with the new way of operating.
This perception issue is the real problem here.
Because the reality is that most of the passenger vehicle sector went high-tech years ago. So, these same people who are resisting change at work are already familiar with modernized, streamlined service experiences for their own, personal vehicles.
They’re used to getting great service experiences with their vehicles but -- for some reason -- they don’t expect a modern, amazing experience from truck service.
Their expectation is backwards. And it doesn’t make sense.
I get it that it’s scary to contemplate going all-in with SRM, especially if your fleet or shop has been doing fine up to this point. I completely understand the if-it-ain’t-broke-don’t-fix-it mindset.
But, I’ve also seen people with this old-school mindset become true believers once they get a taste of the great things that can happen when they unleash the power of SRM for their own operations.
Try it.
Go paperless. Put Decisiv SRM in place, and see what happens when you let your techs be great techs -- using their skills to get work done instead of wasting time pushing papers and chasing entries in logbooks.
With an SRM process in place, you’re improving the standards throughout your entire shop. By laying out the process steps in a logical and methodical sequence until they become automatic, second-nature behaviors, even the youngest and newest technicians will get lost less often.
That bears repeating: The promise of SRM is that most of your techs (in the neighborhood of 80%) will become better at their jobs. They’ll work with more precision and efficiency – they’ll get better and better at their jobs, and they’ll like the way it feels. Plus, asset managers and manufacturers will see higher profits, as asset availability increases by an average of 20%, and triage time is reduced by an average of 70%.
There are quite a few shops that have made this leap of faith. And they have happy techs and higher profits to show for it.
Decisiv SRM offers a range of customizable solutions to help elevate operations of all sizes. If you’re ready to take it to the next level, Decisiv can definitely help.